Grinding Media Distribution Stirred Media Mill
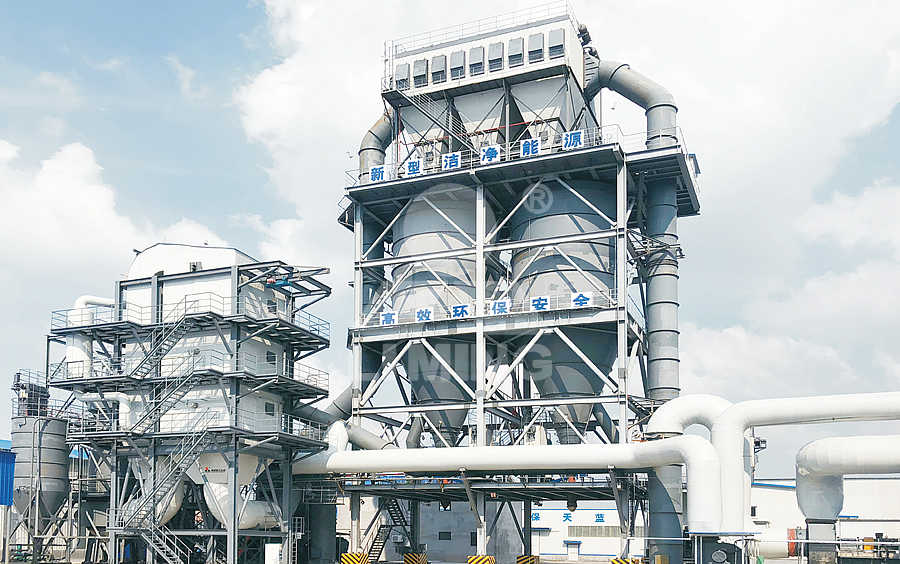
Grinding Media Motion and Collisions in Different Zones of Stirred
2021年2月11日 — Product fineness during grinding in stirred media mills is mainly influenced by the specific energy input, the stress energy transferred by the colliding grinding media 2020年6月1日 — Stirred media mills are increasingly replacing ball mills for fine and ultrafine grinding, typically having around 30–40% less power consumption than ball mills when Stirred media mills in the mining industry: Material 2022年7月1日 — Based on these insights, the grinding media in the stirred media mill are pressed into the holes of the discs, accelerated there to the local circumferential speed Effects of axial grinding media distribution on the disc wear 2004年12月10日 — It is shown that an analysis of the grinding mechanism as well as the energy transfer mechanisms in a stirred media mill enables a general understanding of Stress energy distribution in different stirred media mill
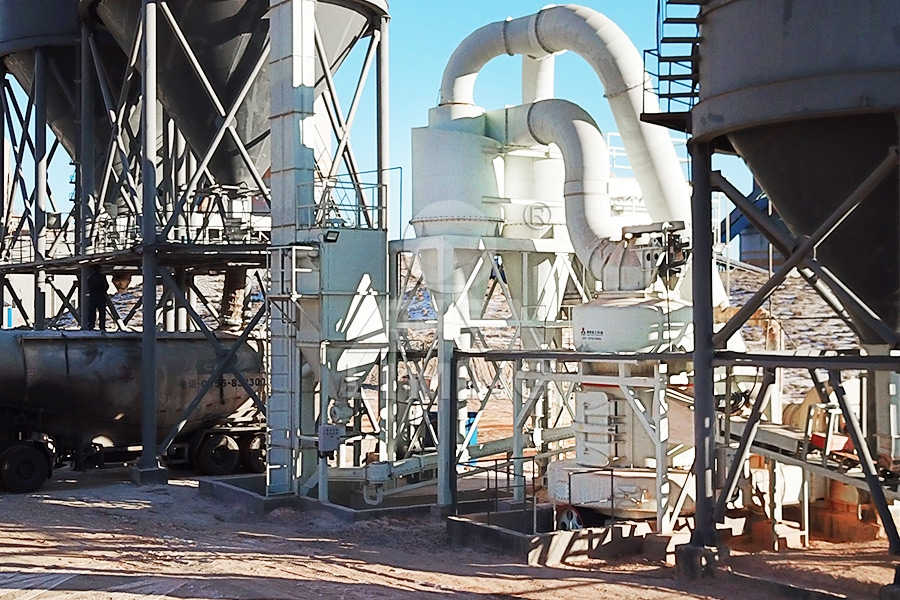
Grinding Media Motion and Collisions in Different Zones
2021年2月11日 — The stress energy from grinding media collisions is heterogeneously distributed in stirred media mills Herein, in order to characterize the stress energy 2017年8月26日 — The stirred media mill principle is the setting into motion of grinding media by means of a rotating agitator, which transfers kinetic energy to the media The feed Development of an Energy Optimized Stirred Media 2021年1月9日 — The stirred media mill model is used to predict the mill power consumption, dynamics of both grinding fluid and grinding media, interparticle contacts of the grinding media, and the wear development A Novel ParticleBased Approach for Modeling a 2020年6月21日 — For a continuous grinding process within a stirred media mill a dynamic model needs to account for the particle transport and the axial grinding media distribution Dynamic Process Models for Fine Grinding and Dispersing
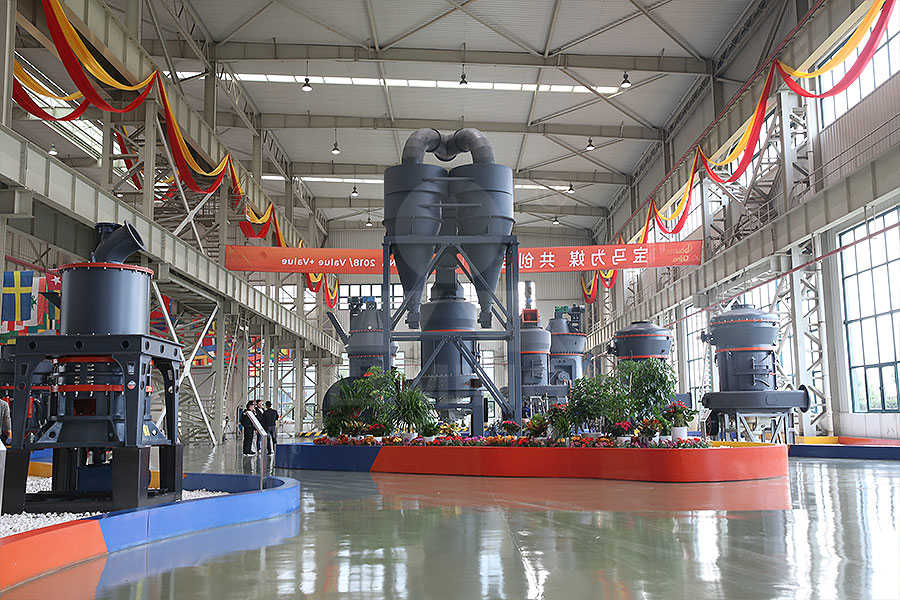
Effects of axial grinding media distribution on the disc wear
2022年7月1日 — Stirred media mills belong to the group of mills with free movable grinding media Stirred media mills are used for dispersion and deagglomeration processes as 2022年7月1日 — In the case of stirred media mills, wear occurs most frequently on the stirrer and the mill liner, besides the grinding media which show the highest wear (Becker, 1999)Due to high throughputs combined with mostly high solids concentrations of the slurry usually desired for productionscale plants, the grinding media tend to be transported Effects of axial grinding media distribution on the disc wear 2022年7月1日 — These observations were made for both, small laboratoryscale and productionscale plants (Becker et al, 2001, Stender et al, 2004, Anymadu et al, 2007) During wet grinding operations in stirred media mills, the grinding media and feed material can cause wear to the process unitEffects of axial grinding media distribution on the disc wear 2007年12月31日 — This chapter discusses the design, physical fundamentals, grinding behavior, operating behavior and scaleup of stirred media mills The chapter shows possibilities to develop new and optimize Chapter 6 Wet Grinding in Stirred Media Mills Request PDF
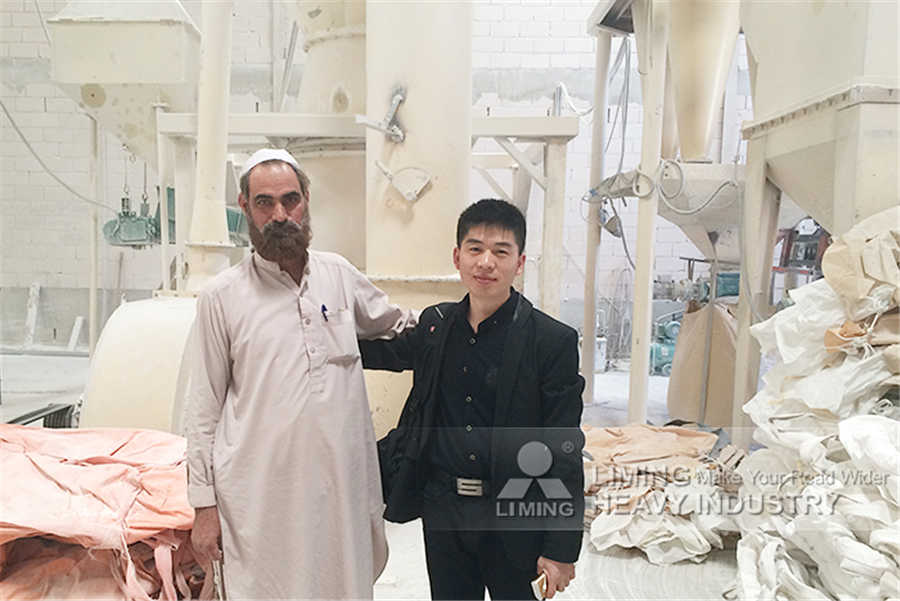
Motion and stress intensity of grinding beads in a stirred media mill
DOI: 101016/00325910(95)030387 Corpus ID: ; Motion and stress intensity of grinding beads in a stirred media mill Part 1: Energy density distribution and motion of single grinding beads2024年7月1日 — Previous studies compare the milling performance of different media sizes [12]Mankosa, Adel and Yoon [13] were one of the first groups to do this by investigating the effects of media size within a lowspeed stirred mill (200–330 rpm) They concluded that the optimal ball size to particle feed size ratio was 20:1 and although this was for dry coal, Segregation in binary and polydisperse stirred media mills 1996年1月1日 — Most industrial vertical stirred mills contain a nonuniform set of grinding media sizes However, this fact is often ignored in simulations, which mostly use monodispersed media The paper explores the fundamental dynamics of vertical mills when using multiple sizes of grinding media, by using DEM simulationMotion and stress intensity of grinding beads in a stirred media mill 2011年1月1日 — Little work has been done in studying the effect of media shape on grinding Existing studies focus on grind performance in ball mills The effect of nonroundness of the feed rock in tumbling mills was first considered in DEM by Cleary (2001b) with mild increases in shoulder position and power draw observed at subcritical mill speeds Is media shape important for grinding performance in stirred mills
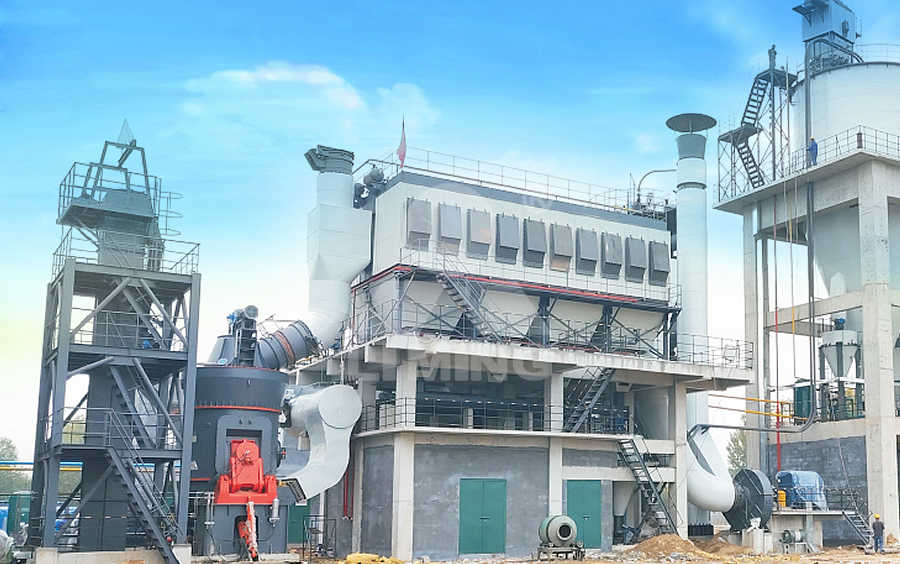
Stirred media mills in the mining industry: Material
2020年6月1日 — Stirred media mills are used by the mining industry for ultrafine grinding to enhance liberation, and to decrease particle sizes of industrial minerals to tailor functional properties This review describes stirred media mill technologies and operating principles, and summarises stress intensity theory which can be used for selecting efficient 2024年6月26日 — 31 Effect of Mill Parameters Figure 1 shows the particle size distributions of milled products at different times using 10 mm grinding balls and a rotation speed of 1000 rpm The bimodal size distribution was observed, especially at long milling times The presence of two peaks, at fine size range and coarse size range, is an indicator of the Effect of Milling Variables on Particle Deformation in a Stirred Media Mill2023年9月21日 — look to the use of coarser media within a stirred mill for coarser feed size applications Due consideration must be given to the grinding density and media size selection for the feed size and final product size To enable use of the vertical stirred mill, the transfer size must be controlled by closing the upstream with aRECENT DEVELOPMENTS IN COARSE GRINDING USING 2021年4月1日 — Several types of the grinding media have been used in stirred mills These include, but are not limited to, glass balls, ceramic balls, steel balls, zirconium balls, and river sand He et al [8] found that the severe wear of glass balls during grinding indicated that they were unsuitable and uneconomical as grinding mediaEffect of grinding media properties and stirrer tip speed on
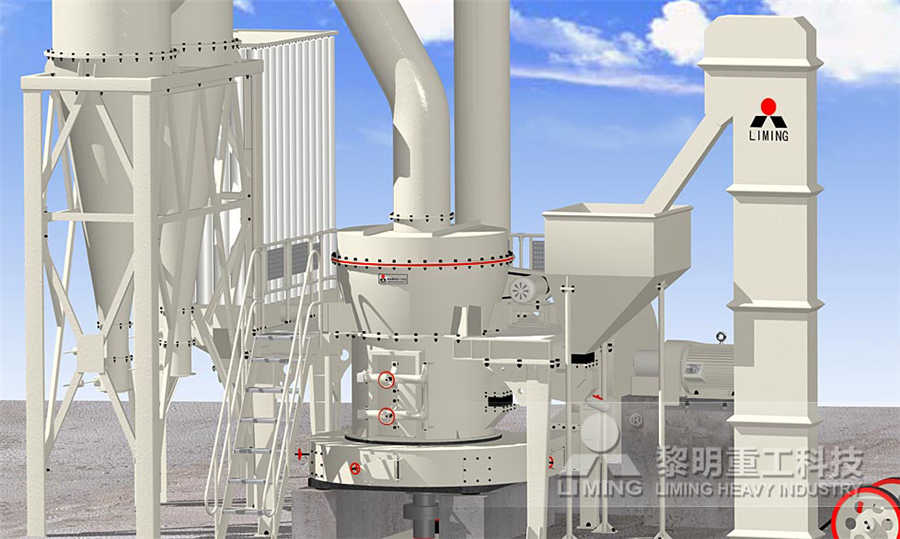
[PDF] Numerical modelling of grinding in a stirred media mill
DOI: 101016/JCES200912003 Corpus ID: ; Numerical modelling of grinding in a stirred media mill: Hydrodynamics and collision characteristics @article{Gers2010NumericalMO, title={Numerical modelling of grinding in a stirred media mill: Hydrodynamics and collision characteristics}, author={Romain Gers and Eric 2004年12月1日 — The relative motion and collision between grinding media in a wetstirred accelerator mill are modelled using the discrete element method (DEM) coupled with computational fluid dynamics (CFD)Stress energy distribution in different stirred media mill 2021年1月8日 — Fine grinding in stirred media mills is an important process in mineral, chemical and pharmaceutical industry The stressing mechanism in these mills is grinding through compression and shearing Experimental assessment of grinding bead velocity 2010年8月18日 — IsaMill™ is a highspeed stirred mill used in the mineral industry for a range of milling duties from ultrafine to coarse grinding In this work, numerical simulations based on the discrete Effects of disc rotation speed and media loading on particle

Effect of operating conditions on the particle size distribution
2022年1月1日 — Stirred mills have been wildly used in mineral processing, chemical products, and other industries due to their higher tip speed, higher filling rate, and smaller media size etc, especially in particle size of ground products below 100 µm (Heath et al, 2017, Jankovic, 2003, Tang et al, 2022)The main evaluation of stirred mill performance 2021年1月9日 — Modeling of wet stirred media mill processes is challenging since it requires the simultaneous modeling of the complex multiphysics in the interactions between grinding media, the moving internal agitator elements, and the grinding fluid In the present study, a multiphysics model of an HIG5 pilot vertical stirred media mill with a nominal power of 75 A Novel ParticleBased Approach for Modeling a Wet Vertical Stirred 2021年2月1日 — Fine grinding in stirred media mills is an important process in mineral, chemical and pharmaceutical industry (Netzsch/Glencore) was used to study the effect of fluid viscosity and volume flow rate on the grinding bead velocity distribution in stirred media mills measured by magnetic tracking The mill consists of six perforated discs in a Experimental assessment of grinding bead velocity 2024年8月1日 — Typically, grinding media are not accelerated to the tip speed of the mill Different studies reveal that the minimum grinding media tangential velocities are in the range of 30 to 50% of the tip speed [[49], [50], [51], [52]]Hence, there are several approaches to account for this effect by using specially defined factors [1, 53]Stender et Improved energy transfer model for mechanistic scaleup of stirred
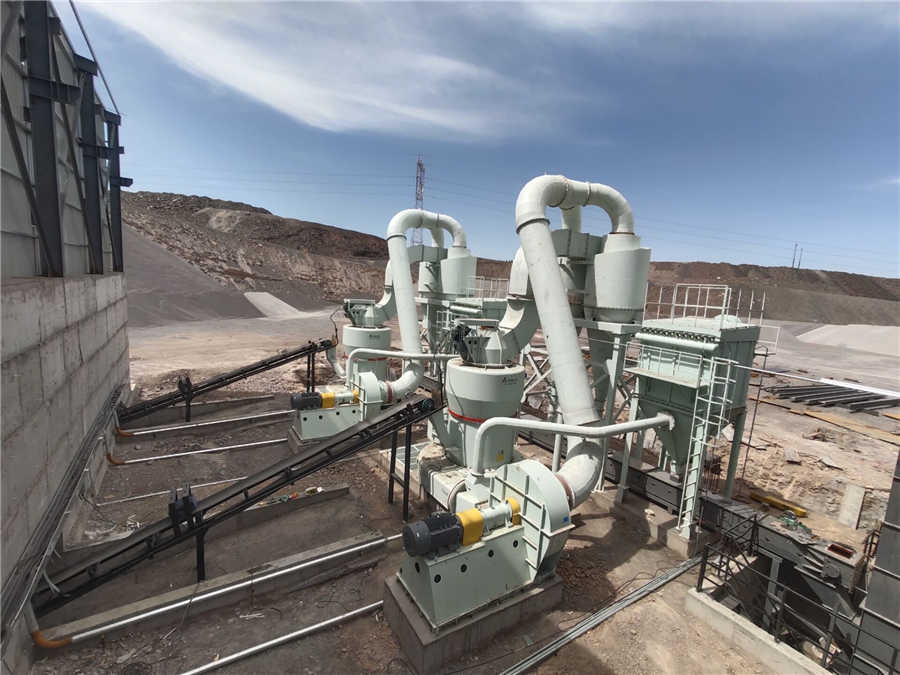
Product size distribution in stirred media mills ScienceDirect
2000年4月1日 — The results indicated that the slope of product size distribution can be controlled by altering some operating parameters, such as size of grinding media and tip or peripheral speed The profile of product size distribution from the stirred media mills was found to follow most closely the RosinRammlerBennett (RRB) model2020年5月1日 — Stirred media mills are used by the mining industry for ultrafine grinding to enhance liberation, and to decrease particle sizes of industrial minerals to tailor functional propertiesStirred media mills in the mining industry: Material 2000年4月1日 — The profile of product size distribution from the stirred media mills was found to follow most closely the RosinRammlerBennett (RRB) model on dry grinding of barite (BaSO4, d50= 283 µm Product Size Distribution in Stirred Media Mills Request PDF2010年9月1日 — Nanoparticles can be produced by wet grinding in stirredmedia mills In the lower nanometer range a true grinding limit exists, where the transferred energy from the grinding media is no longer Nanoparticle Production with Stirred‐Media Mills:
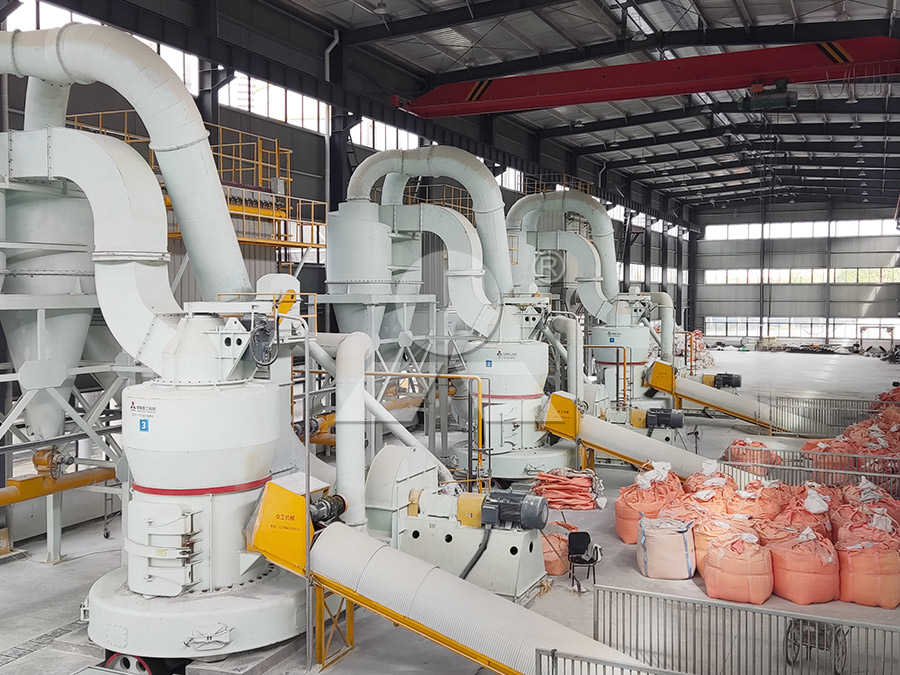
Impact of grinding aids and process parameters on dry stirred media
2018年7月15日 — The impact of the stress conditions inside the mill on the grinding result was examined by varying the media size d GM, grinding media density ρ GM and stirrer tip speed v tTherefore, three different kinds of grinding media materials as well as a number of media sizes were investigated in this study (see Table 1), while the grinding media filling 2020年6月21日 — In the past century, many research studies have investigated the stressing conditions in stirred media mills Researchers developed a broader and better understanding of breakage mechanisms and breakage energy used in stirred media mills [3,4,5,6]Since the process optimization is a timeconsuming process due to several experiments that Dynamic Process Models for Fine Grinding and Dispersing2022年3月10日 — The relative motion and collision between grinding media in a wetstirred accelerator mill are modelled using the discrete element method (DEM) coupled with computational fluid dynamics (CFD)(PDF) Simulation of Grinding Media Motion and Collisions in 2010年9月15日 — IsaMill™ is a highspeed stirred mill used in the mineral industry for a range of milling duties from ultrafine to coarse grindingIn this work, numerical simulations based on the discrete element method (DEM) were performed to investigate the particle flow in a dry stirred mill with a similar configuration to that of an IsaMill™ The effects of Effects of disc rotation speed and media loading on particle
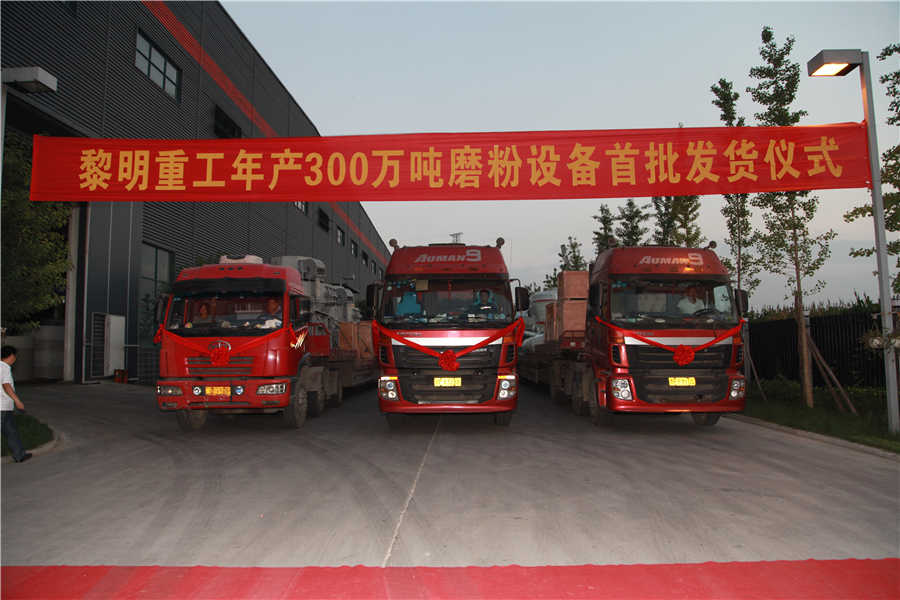
The Influence of Stirred Mill Orientation on Calcite Grinding
The purpose of this study was to investigate the dry grindability of calcite powders in a vertically and horizontally orientable laboratory batch type stirred mill The experimental results were evaluated using stress intensity analysis The performance was also compared in terms of mill orientation The results showed that the d50 values decreased with 2023年9月1日 — Stirred media mills exhibit energysaving benefits at similar grinding levels while providing a broader particle size distribution [16] This is attributed to the highdensity frictional force within the mill, resulting in the production of finer particlesStirred media mill: A novel efficient technology for 2014年6月12日 — The article deals with an innovative approach of combining modern simulation techniques with pilot plant testing work with the target to develop a new stirred media grinding mill With the help of discrete element simulation various mill configurations were studied The target was maximizing the interactions between beads and the related Development of an Energy Optimized Stirred Media Grinding Mill2004年11月1日 — Numerical calculations concerning the flow field, the distribution of the specific energy and the motion of single grinding beads in the grinding chamber of a stirred media mill have been carried outMeasurement of the motion of grinding media in a vertically stirred
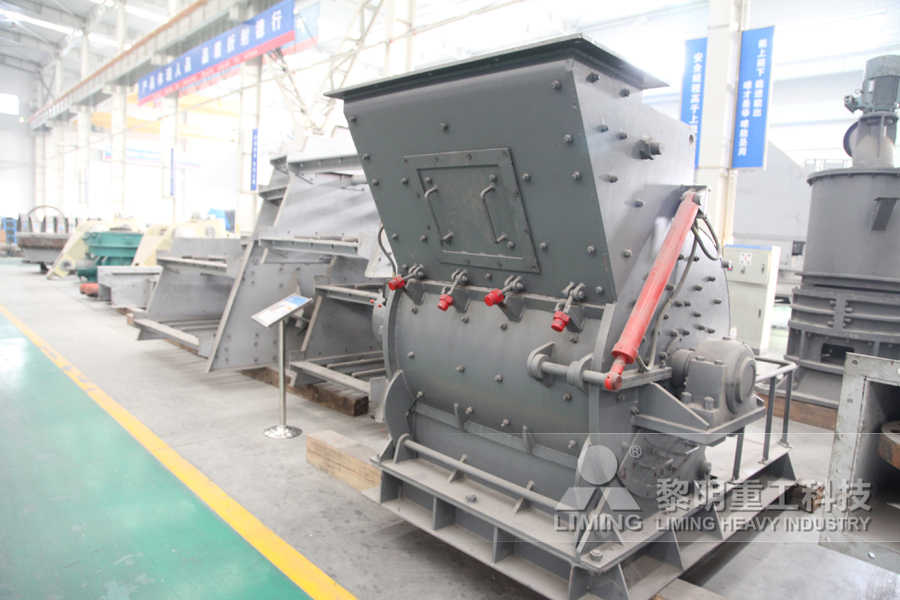
Wet grinding of CaCO3 with a stirred media mill: Influence of
2015年3月31日 — Chemical and process industries utilize stirred media mills for efficient fine grinding of solids Stirred media mills, also referred to as stirred ball or stirred bead mills, generally have a Product fineness during grinding in stirred media mills is mainly influenced by the specific energy input, the stress energy transferred by the colliding grinding media and the stress frequency The stress energy from grinding media collisions is heterogeneously distributed in stirred media mills Herein, in order to characterize the stress energy distribution and the Grinding Media Motion and Collisions in Different Zones of Stirred 2020年3月15日 — The media velocity distribution and the position of its maximum were expected to be affected by the impeller design, specifically by the arms' length, and the simulations were used to capture this effect Measurement of the motion of grinding media in a vertically stirred mill using positron emission particle tracking (PEPT) Miner Eng, 15 Investigating grinding media dynamics inside a vertical stirred mill 2024年4月1日 — As a result, the difference between the 5pin vertical and 5pin horizontal settings was attributed to the mill's grinding media distribution and powder caking, Determination of the most important grinding mechanism in stirred media mills by calculating stress intensity and stress number Powder Technol, 105 (1999), pp 382388The impact of different stirrer designs and mill orientations
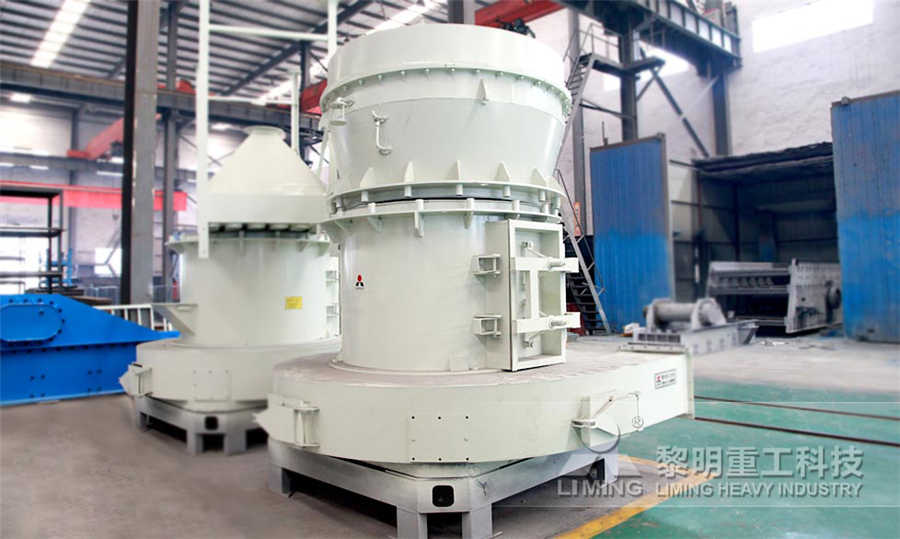
Experimental evaluation of the energy transfer within wet
2023年7月1日 — Within stirred media mills, the comminution process is based on collisions of grinding media Depending on the field of application, there are different types, designs and sizes of stirred media mills, although the general principle of operation is in most cases identical Fig 1 shows the schematic of a stirred media mill The shaft of the 2018年9月24日 — One of the most energyintensive processes for producing submicron range calcite is stirred media mill In the present work, numerous operating parameters such as solid mass fraction, grinding media size, media filling ratio, and grinding time have been investigated using a vertical type stirred media mill The results are evaluated on the Effect of Operating Parameters on the Breakage Process of 1999年11月1日 — The importance of stirred media mills in various industries and in research is steadily increasing The comminution process in these mills is determined mainly by the number of stress events in the grinding chamber and by the intensity acting at these stress events: for a certain stress intensity a certain relation between the product fineness and Wet comminution in stirred media mills ScienceDirectDOI: 101016/JMINPRO200407003 Corpus ID: ; Stress energy distribution in different stirred media mill geometries @article{Stender2004StressED, title={Stress energy distribution in different stirred media mill geometries}, author={H Stender and Arno Kwade and J{\"o}rg Schwedes}, journal={International Journal of Mineral Processing}, Stress energy distribution in different stirred media mill

Mill, material, and process parameters ScienceDirect
2019年8月1日 — The grinding limit or minimum particle size can be calculated from intercrystalline material parameters as described by Knieke et al [55]The compression strength σ CS is a material parameter, and was used based on the assumption that compression is the dominant type of stress in a stirred media mill The compression strength and 2022年7月1日 — In the case of stirred media mills, wear occurs most frequently on the stirrer and the mill liner, besides the grinding media which show the highest wear (Becker, 1999)Due to high throughputs combined with mostly high solids concentrations of the slurry usually desired for productionscale plants, the grinding media tend to be transported Effects of axial grinding media distribution on the disc wear 2022年7月1日 — These observations were made for both, small laboratoryscale and productionscale plants (Becker et al, 2001, Stender et al, 2004, Anymadu et al, 2007) During wet grinding operations in stirred media mills, the grinding media and feed material can cause wear to the process unitEffects of axial grinding media distribution on the disc wear 2007年12月31日 — This chapter discusses the design, physical fundamentals, grinding behavior, operating behavior and scaleup of stirred media mills The chapter shows possibilities to develop new and optimize Chapter 6 Wet Grinding in Stirred Media Mills Request PDF
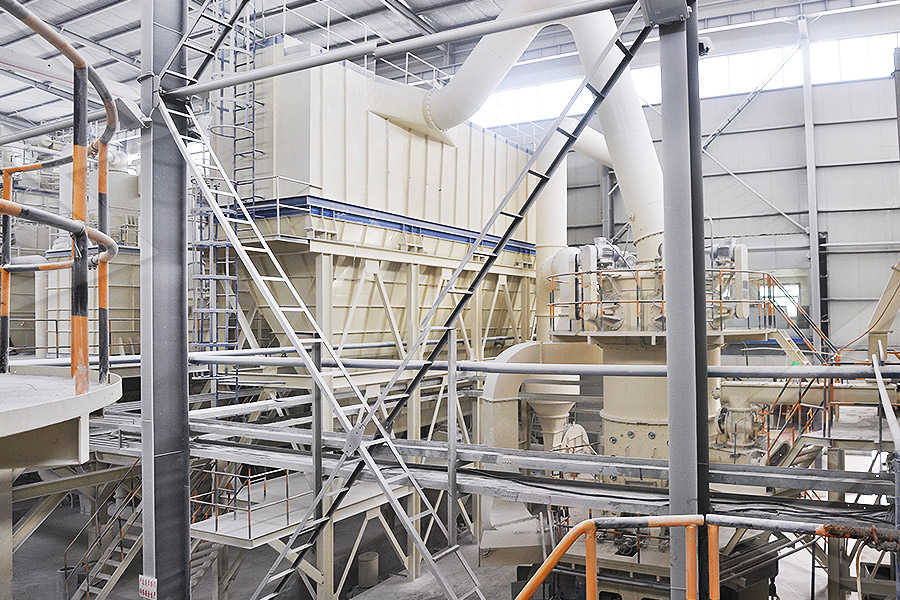
Motion and stress intensity of grinding beads in a stirred media mill
DOI: 101016/00325910(95)030387 Corpus ID: ; Motion and stress intensity of grinding beads in a stirred media mill Part 1: Energy density distribution and motion of single grinding beads2024年7月1日 — Previous studies compare the milling performance of different media sizes [12]Mankosa, Adel and Yoon [13] were one of the first groups to do this by investigating the effects of media size within a lowspeed stirred mill (200–330 rpm) They concluded that the optimal ball size to particle feed size ratio was 20:1 and although this was for dry coal, Segregation in binary and polydisperse stirred media mills 1996年1月1日 — Most industrial vertical stirred mills contain a nonuniform set of grinding media sizes However, this fact is often ignored in simulations, which mostly use monodispersed media The paper explores the fundamental dynamics of vertical mills when using multiple sizes of grinding media, by using DEM simulationMotion and stress intensity of grinding beads in a stirred media mill 2011年1月1日 — Little work has been done in studying the effect of media shape on grinding Existing studies focus on grind performance in ball mills The effect of nonroundness of the feed rock in tumbling mills was first considered in DEM by Cleary (2001b) with mild increases in shoulder position and power draw observed at subcritical mill speeds Is media shape important for grinding performance in stirred mills
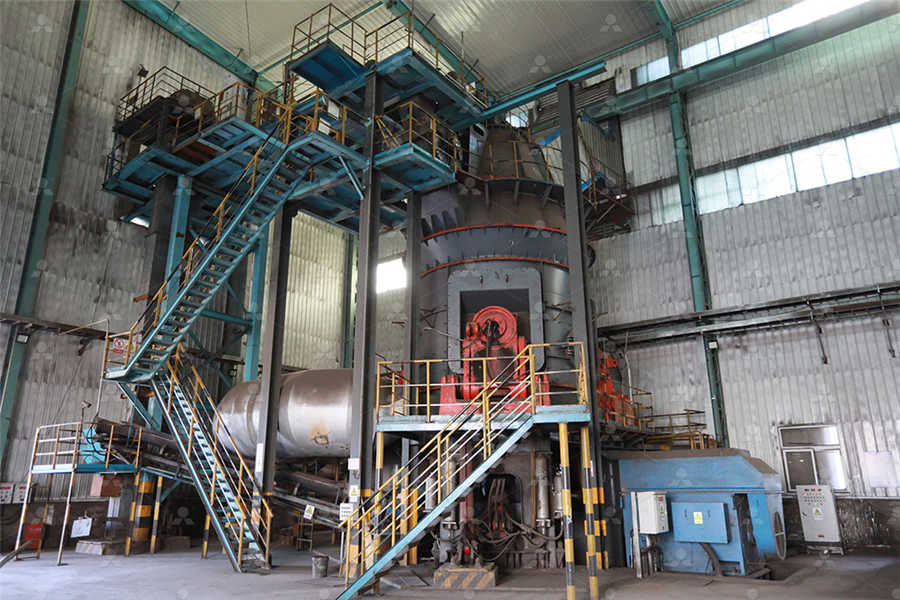
Stirred media mills in the mining industry: Material
2020年6月1日 — Stirred media mills are used by the mining industry for ultrafine grinding to enhance liberation, and to decrease particle sizes of industrial minerals to tailor functional properties This review describes stirred media mill technologies and operating principles, and summarises stress intensity theory which can be used for selecting efficient 2024年6月26日 — 31 Effect of Mill Parameters Figure 1 shows the particle size distributions of milled products at different times using 10 mm grinding balls and a rotation speed of 1000 rpm The bimodal size distribution was observed, especially at long milling times The presence of two peaks, at fine size range and coarse size range, is an indicator of the Effect of Milling Variables on Particle Deformation in a Stirred Media Mill2023年9月21日 — look to the use of coarser media within a stirred mill for coarser feed size applications Due consideration must be given to the grinding density and media size selection for the feed size and final product size To enable use of the vertical stirred mill, the transfer size must be controlled by closing the upstream with aRECENT DEVELOPMENTS IN COARSE GRINDING USING